Идеальный сварной шов: как определить качество
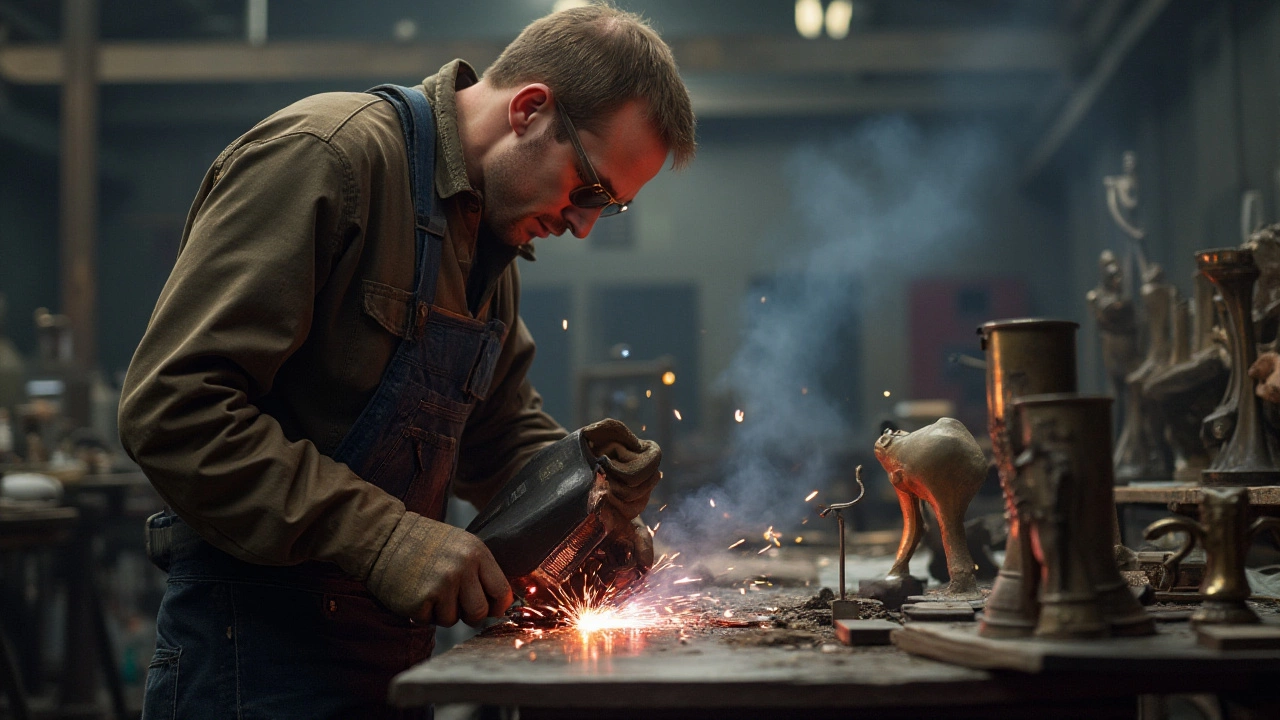
Сварочные работы занимают важное место в различных отраслях, от строительства до автомобилестроения. От качества сварного шва зависит надежность и долговечность конструкций. Но как отличить хороший сварной шов от плохого? На что стоит обратить внимание, чтобы быть уверенным в качестве и безопасности соединения?
Эти вопросы волнуют не только профессионалов, но и любителей, работающих с металлом. В данной статье мы рассмотрим, какие характеристики свидетельствуют о хорошем сварном шве, а также предоставим практические советы, которые помогут достичь наилучшего результата.
- Внешний вид хорошего шва
- Технические требования к сварным соединениям
- Методы проверки качества сварки
- Типичные ошибки и как их избежать
- Советы по улучшению качества сварки
- Профессиональные рекомендации
Внешний вид хорошего шва
Когда речь заходит о сварочных работах, внешний вид сварного шва — это первое, что привлекает внимание как профессионала, так и заказчика. Хороший шов должен быть равномерным и однородным, без видимых дефектов. Прежде всего, обратите внимание на гладкость поверхности шва. Что значит «гладкий»? Это означает отсутствие пор, трещин и других поверхностных изъянов. Такой шов выглядит целостным, словно единое целое с основным металлом.
Правильная форма сварного шва — еще один важный критерий. Идеально, если шов представляет собой аккуратную, симметричную линию. При ручной дуговой сварке эта задача может показаться сложной, однако профессиональный сварщик знает, как добиться такого результата благодаря опытным навыкам и точной настройке сварочного оборудования. Сам по себе шов должен быть немного выпуклым или плоским, но не вогнутым, что говорит о недостаточной проплавке.
Проверяя качество сварки, важно обратить внимание на отсутствие лишнего металла, известного как «утюжок» или «грата». Эти выпуклости или наплывы на краях шва образуются из-за избыточного материала и говорят о неправильных настройках сварочного тока. Опытный сварщик тщательно выравнивает количество материала, чтобы избежать этих дефектов, которые ухудшают не только визуальную составляющую, но и прочностные характеристики соединения. Известная цитата одного из профессиональных сварщиков гласит:
"Хороший шов — это не только о красоте, но и о долговечности антунных связей."
Не забудьте оценить также симметрию шва. Это может быть непросто на первых порах, но четкое внимание к деталям и практика помогут. Симметричный шов распределяет напряжение равномерно, уменьшая риск ослабления конструкции в процессе эксплуатации. Еще один фактор — цвет шва. Он должен быть однообразным по своей длине и не слишком темным, что может говорить о перегреве стали.
Технические требования к сварным соединениям
Качественное сварочное соединение требует соблюдения ряда технических стандартов, которые варьируются в зависимости от материала, метода сварки и ожидаемых нагрузок на конструкцию. Одним из ключевых аспектов является выбор правильного материала для заполнения шва, который должен соответствовать механическим свойствам основных элементов. Это гарантирует долговечность и надежность соединения. Еще один важный момент - толщина и ширина шва, которые напрямую влияют на нагрузку, которую конструкция способна выдержать.
Главное, что следует понимать при работе со сварными соединениями — это то, как важна их геометрическая точность. Правильная форма и глубина шва могут предотвратить появление дефектов, таких как трещины или проплавления. Длина шва должна быть равномерной, без резких перетоков, которые могут ослабить конструкцию. Кроме того, поверхность шва должна быть чистой, без шлаковых включений или пор, которые снижают адгезию соединения.
"Соблюдение стандартов и технических требований при сварке гарантирует безопасные условия эксплуатации и спасает жизни," — отмечает Игорь Петров, эксперт в области сварочных технологий.
Создавая качественный сварочный шов, важно придерживаться международных стандартов, таких как AWS (American Welding Society) или ISO (International Organization for Standardization). Эти нормы задают параметры, которые оговаривают не только внешний вид шва, но и требования к его внутренней структуре. Это подразумевает использование методов неразрушающего контроля, таких как ультразвуковое сканирование или рентгеновский анализ, для проверки целостности соединения.
Контроль температуры сварки — еще один критически важный аспект. Если температура слишком высока, это может привести к выгоранию легирующих компонентов, что негативно скажется на коррозионной стойкости и прочности. Напротив, недостаточная температура может вызвать неполное плавление металла, образуя холодные соединения, что нежелательно для качества сварки.
Стоит отдельно выделить область теплового влияния, которая может изменять микроструктуру металла в месте сварки, и тем, кто занимается профессиональными сварочными работами, необходимо постоянно учитывать эти изменения для сохранения оптимальных параметров. Этот фактор особенно значим в конструкциях, подверженных циклическим нагрузкам или работающих при экстремальных температурах.
Эффективная технология сварки также предусматривает полный контроль над внешними условиями в процессе работы. Влажность, ветер, наличие загрязняющих веществ в воздухе — все это способно повлиять на качество сварной ванны и последующего шва. Небрежное отношение к этим деталям может увеличить количество дефектов и снизить прочность готового изделия.
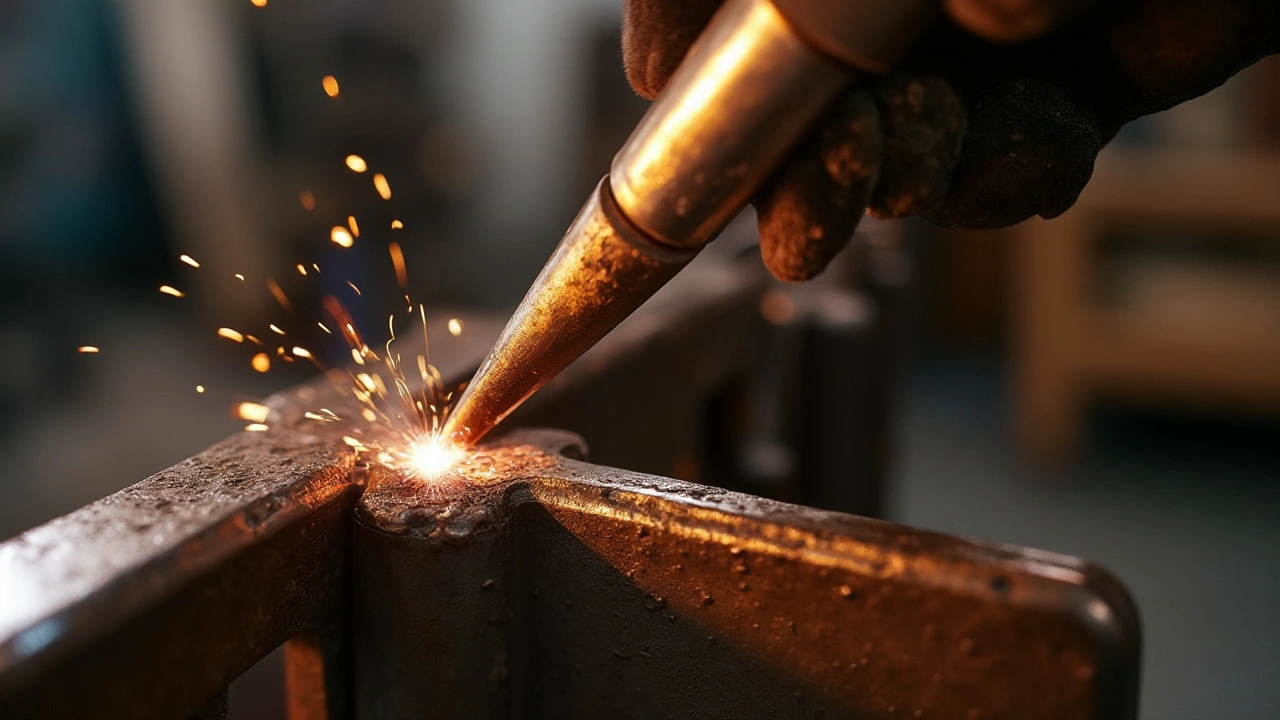
Методы проверки качества сварки
Качество сварочного шва — это не просто эстетический аспект, хотя внешний вид тоже имеет значение. Хороший сварочный шов гарантирует прочность и долговечность конструкции, а также безопасность её эксплуатации. Для проверки качества сварочных соединений существует множество методов, начиная от визуального осмотра и заканчивая сложными техническими испытаниями. Один из простейших, но важных шагов — это тщательный визуальный осмотр. На этом этапе оцениваются такие параметры, как равномерность шва, отсутствие дефектов и пор. Опытный глаз мастера может быстро определить, соответствует ли шов нормам.
Инженер-сварщик Алексей Иванов отмечает: "Визуальный осмотр остаётся важной первой линией защиты. Он позволяет выявить многие проблемы на начальных этапах производства".
Когда внешний вид сварочного шва изучен, применяются неразрушающие методы контроля. Это методы, которые позволяют определить состояние материала без его повреждения. Среди таких методов наиболее распространёнными являются радиографический и ультразвуковой контроль. Радиографическая проверка предусматривает использование рентгеновских лучей или гамма-излучения, что позволяет выявить внутренние дефекты шва. Ультразвуковой анализ, в свою очередь, более безопасен и удобен, так как не требует использования радиации. Он основывается на принципе отражения ультразвуковых волн от границ дефектов. Эти две технологии нередко применяются совместно для повышения точности диагностики. Проверка сварки с их помощью становится более достоверной.
Далее, следует упомянуть методы разрушающего контроля. Здесь исследование осуществляется на выборочных образцах, которые подвергаются механическим испытаниям. Обычно это испытания на растяжение, ударную вязкость и усталостную прочность. Метод довольно эффективен, но из-за своей разрушительной природы он используется только для отдельных образцов или испытательных партий. Эти данные помогают понять, какие нагрузки может выдержать соединение, что критически важно для объектов с высокой ответственностью.
Контролируя качество сварки на всех этапах, можно повысить надежность и безопасность конструкции. Необходимо помнить, что каждый из методов имеет свои преимущества и недостатки, поэтому наилучших результатов можно добиться за счет их комбинирования. На производственных участках обычно внедряют процедуры контроля, охватывающие сразу несколько техник. Это гарантирует комплексный подход к качеству.
Типичные ошибки и как их избежать
Сварочные работы требуют внимания к деталям и немалого опыта. Ошибки, которые допускают как новички, так и опытные специалисты, могут сильно повлиять на качество сварки. Одна из распространённых ошибок — недостаточная очистка поверхности перед началом работы. Если металл не очищен от ржавчины, краски или масла, это может вызвать дефекты, такие как пористость или непроварку. Перед началом процесса сварки крайне важно тщательно подготовить поверхности, чтобы обеспечить их чистоту и свободное взаимодействие.
Еще одной серьёзной ошибкой является неправильный выбор технологических параметров сварки, таких как сила тока и скорость подачи проволоки. Неправильно выставленные параметры могут привести к перегреву металла, образованию брызг и даже повреждению свариваемых деталей. Сварщик должен тщательно подбирать параметры в зависимости от толщины металла и типа используемой сварочной проволоки. Это часто требует практического опыта и понимания особенностей конкретных материалов.
"Успех в сварке во многом зависит от подготовки, — говорит Владимир Смирнов, инженер-технолог с опытом более 20 лет. — Лучше потратить больше времени на настройку оборудования и проверку параметров, чем потом исправлять допущенные ошибки".
Нарушение техники безопасности также входит в список типичных ошибок. Часто сварщики забывают использовать защиту для глаз и кожи, что ведёт к травмам. Напоминаем, что всегда необходимо применять средства индивидуальной защиты и следить за безопасностью окружающих. Правильное расположение оборудования и передвижение свариваемых изделий также помогут избежать ненужных проблем и простоев.
В контексте минимизации ошибок стоит упомянуть важность regular осмотра и контроля качества сварки. Опытные сварщики используют неразрушающий метод проверки, такой как ультразвуковая детекция, чтобы убедиться в отсутствии внутренних дефектов. Структурный контроль позволяет обнаружить непрерывные трещины и другие скрытые изъяны. Внедрение регулярных инспекций в производственный процесс помогает своевременно выявить и исправить ошибки, что улучшает конечный результат и увеличивает надёжность сварного соединения.
В заключение, чтобы избежать типичных ошибок в сварочных работах, необходимы полноценная подготовка и соблюдение всех технологических операций. Непрерывное обучение и практика являются ключом к повышению мастерства и качества сварных швов. Так сохранится не только эстетическая красота шва, но и его функциональная надежность в самых сложных конструкциях.
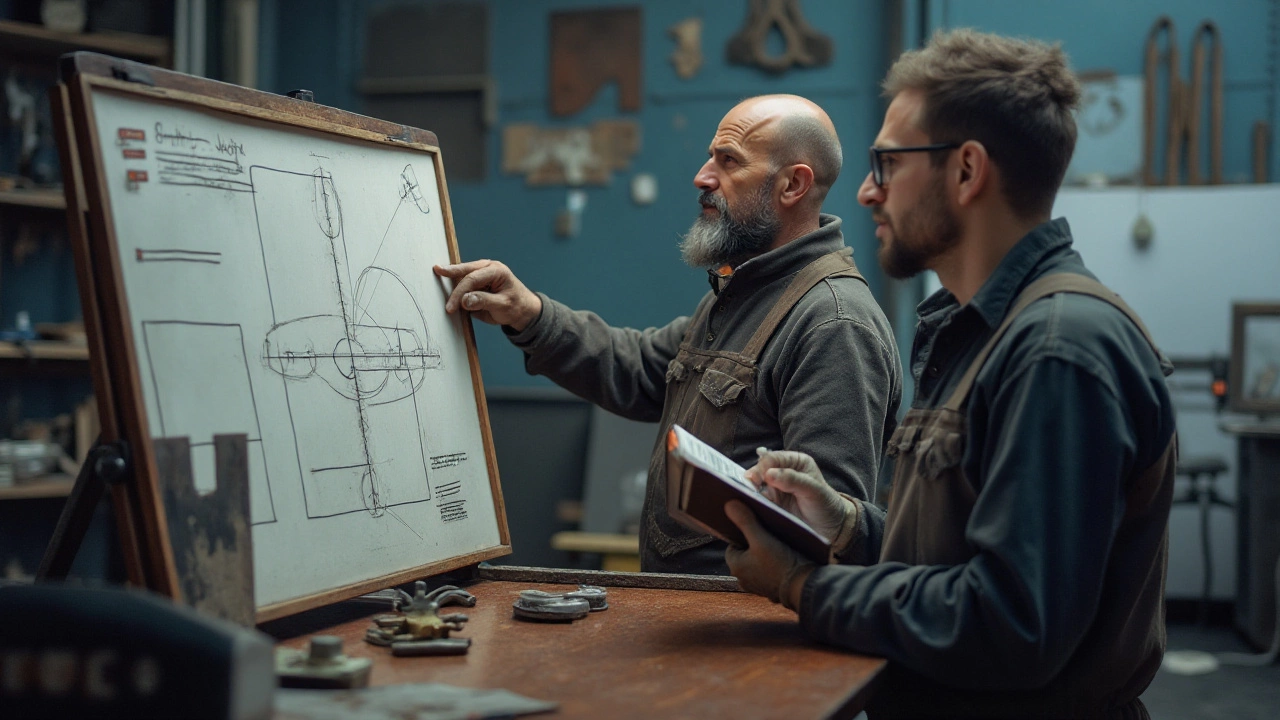
Советы по улучшению качества сварки
Совершенствование качества сварных соединений требует не только технических знаний, но и внимательного подхода к учебному процессу. Умение проверка сварки — это навык, который можно развивать. Всегда полезно изучать новые технологии и методы, даже если вы уже имеете значительный опыт в области сварочных работ. Один из ключевых моментов — это выбор правильного оборудования и материалов. Инвестиции в качественное оборудование могут значительно повлиять на конечный результат. Например, правильная настройка сварочного аппарата играет роль в формировании шва без дефектов.
Технические знания — это основа, но никуда без практики. Регулярное выполнение операций позволяет выработать уверенные движения, что очень важно при выполнении ответственных задач. Обучение у опытных специалистов может стать отличным подспорьем для роста: наблюдение за их работой и разбор их методов помогают глубже понять тонкости каждого этапа. К тому же, они могут предоставить ценные советы по качеству сварки, которые невозможно получить из учебников.
Избегайте частых ошибок
Значительная часть неудач в сварке связана с незнанием шероховатостей процедуры. Допуск ошибок на начальном этапе, таких как неправильный угол подачи электрода или несоответствующая скорость сварки, может привести к образованию дефектов. Проблемы с замаскированными шлаками, которые не всегда заметны невооруженным глазом, часто проявляются позже.
Как сказал один известный сварщик, "Совершенный шов начинается с понимания своих ошибок, а не просто их исправления".Регулярная проверка сварки, включая визуальный осмотр и применение тестов на прочность, также необходима для поддержания высокого уровня качества.
Одним из способов избежать часто встречающихся ошибок является планирование работы. Прежде чем приступить, стоит проанализировать каждый этап процесса и убедиться в наличии всех необходимых материалов и инструментов под рукой. Важность соблюдения правил безопасности также не может быть недооценена — это залог вашей уверенности и здоровья. Правильная планировка пространства и надежная защита от излучения и искр могут предотвратить множество неприятных ситуаций.
Используйте передовые технологии
Современные технологии способствуют ежедневному улучшению сварочного шва. Автоматизация процессов, внедрение роботизированных систем и лазерные технологии значительно повышают точность и скорость выполнения работ, минимизируя человеческий фактор. Использование новейших методов предполагает знакомство с последними достижениями в отрасли и требует постоянного обучения. Статистика подтверждает, что компании, которые вкладывают в инновации, оказываются впереди конкурентов. Это оправдывается не только улучшением качества, но и экономией времени и материалов. Совмещение традиционных методик с новшествами позволяет достичь результативности и долговечности сварного соединения.
Профессиональные рекомендации
Работа сварщика всегда была важной, но не всегда простой. Чтобы добиться идеального сварочного шва, необходимо постоянно совершенствовать свои навыки и быть в курсе новейших технологий. Качество сварки во многом зависит от техники и подхода, используемого в процессе работы. Многие опытные мастера утверждают, что первое, что следует учесть — это правильная подготовка металла и оборудования. Компоненты, которые будут свариваться, должны быть тщательно очищены от загрязнений и заусенцев. Это создает идеальные условия для плотного и надежного соединения, что является основным требованием к качеству сварки.
Также важное место занимает выбор угла и положения сварки. Если, например, сварка ведется в сложных условиях, таких как вертикальные или потолочные швы, лучше всего использовать позиции, которые минимизируют усталость мастера и позволят контролировать качество в процессе работы. Применение различных техник, таких как технология подваривания корня или многопроходной сварки, помогает достичь лучших результатов.
Правильное оборудование и настройки
Выбор оборудования и его корректные настройки играют ключевую роль в достижении качественного результата. Современные аппараты для сварки предоставляют широкий выбор настроек, которые необходимо грамотно использовать. Например, регулировка силы тока или выбора диаметра электрода может существенно повлиять на конечный результат. Очень важно следить за тем, чтобы параметры сварки соответствовали типу используемого металла и толщине соединяемых деталей. Есть мнение, подтвержденное практикой: «Правильная настройка оборудования — залог успеха сварочных работ».
«Эффективность работы сварщика на 60% зависит от его умений и на 40% от умения правильно выбрать и настроить оборудование» — говорит эксперт технической академии Игорь Самойлов.
Немаловажным фактором является применение качественных расходных материалов. От этого напрямую зависит долговечность соединения и его устойчивость к внешним воздействиям. Современные высокотехнологичные электроды и проволока позволяют получать более прочные соединения, что особенно актуально в условиях экстремальных температур и нагрузок.
Непрерывное обучение и практика
Совершенствование навыков — путь к мастерству. Многие профессионалы советуют регулярно проходить курсы повышения квалификации, участвовать в мастер-классах и всегда оценивать свою работу критически. Важно вести архив выполненных задач и анализировать ошибки, чтобы не допускать их в будущем. Для сварщика это не только работа, но и свой вид искусства, где каждая удачно выполненная задача приносит моральное удовлетворение и уверенность в своих силах.
Выводы могут быть разными, но солидарность в одном: без постоянного стремления к самосовершенствованию и следованию профессиональным рекомендациям невозможно достичь настоящего мастерства. Стремитесь к новым высотам, и качество ваших сварочных швов будет повышаться день ото дня, принося уважение коллег и доверие клиентов.
Параметр | Рекомендация |
---|---|
Температура шва | 1200°C - 1500°C |
Сила тока | 100A - 200A |
Диаметр электрода | 2.5 мм - 4.0 мм |